2016年11月7日
こんにちは
営業部の杉本です。
久しぶりの投稿になります。
先日、開発段階の蓄光原料をわけていただきましたので自社製品で蓄光プラスチック樹脂原料の成形テストを行いました。
蓄光原料自体は以前から世間一般にありますが、今回分けていただいた原料は通常の蓄光原料より発光時間が長い事と完全防水で屋外使用可能な事が特徴です。
蓄光原料の純度はおよそ80%が一般的ですが今回の原料は98%と高純度になっており、一般的な蓄光製品が暗闇で約3時間ほどの発光するのに対し今回の原料は約7時間発光し続けます。(蓄光時間や発光性は混ぜ合わせる分量によっても異なります。)
万が一、夜に停電が起きても、朝が来るまで発光しますので、地震などの緊急時の災害対策商品、防災関連グッズとしての需要が見込めます。
停電の際など、暗闇で光るプラスチックでできた表示板などがあれば、出口までの目印になります。
ところで、蓄光プラスチック樹脂材(蓄光原料)とは・・・ベースとなる原料に蓄光顔料や蓄光マスターバッチなどのプラスチック蓄光材を混ぜ合わせた樹脂原料のことを指します。
(今回はポリカーボネートに20%の割合でブレンドしました。)
蛍光灯や自然光などの光を吸収し、蓄えた光エネルギーで発光するので部屋や外が暗くなると効果を発揮する特殊な原料です。
そのため蓄光原料を使用することで、光る樹脂製品を作ることが可能です。余談ですが子供の頃、部屋の天井に星のシールを貼っていました。あれも蓄光ですね。
今回、弊社ネットショップで販売している
「キューブボックスα 木扉鍵付き」に使用する樹脂パーツで射出成形試作を行いました。

■実際に付けてみました。
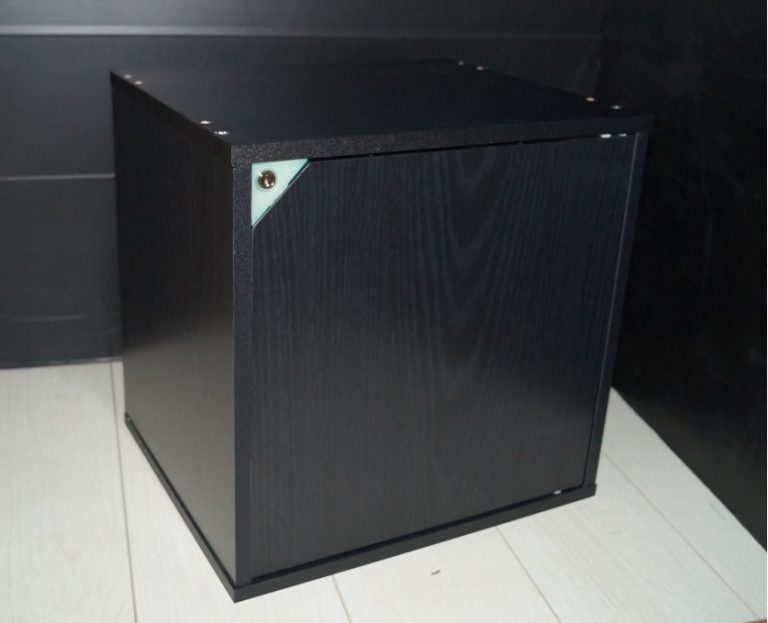
■暗闇ではこのように光ります。
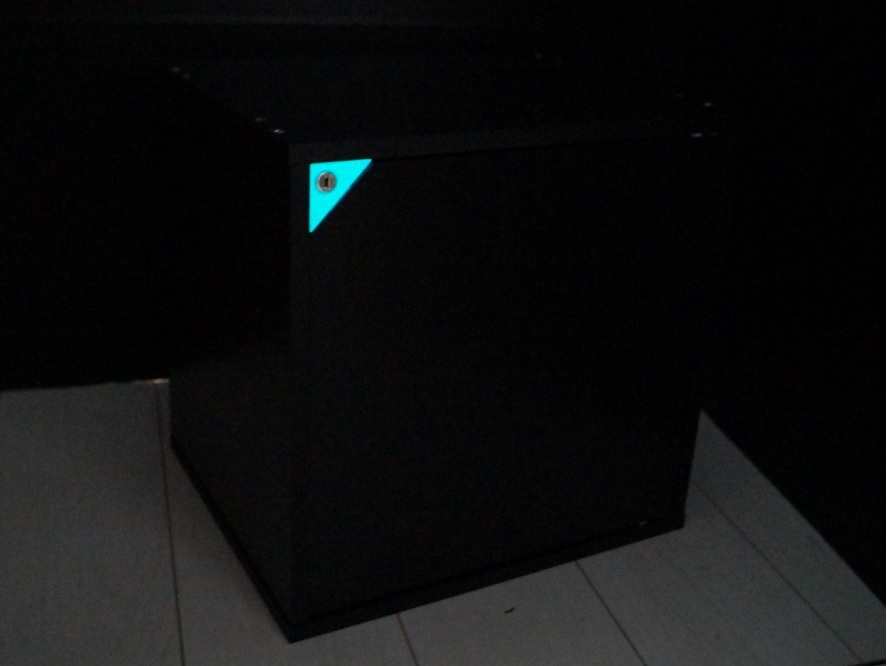
とても綺麗な色で発光しております。
■明るさは一旦落ち着きますが目視でわかる十分な光度です。
■暗闇ではこのように光ります。
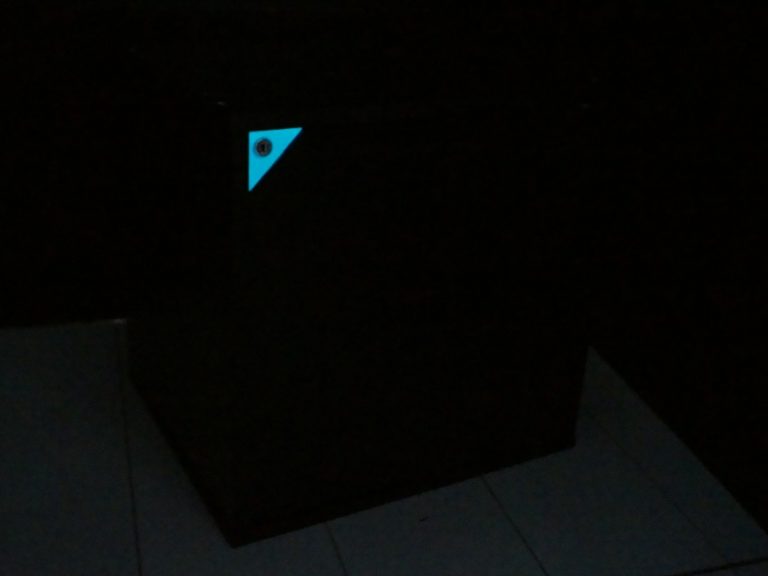
今回の試作で感じたことをまとめます。
蓄光原料を使った製品の成形条件について
■使用原料のベースはPC(ポリカーボネート)でしたが、通常の成形条件で問題無く作成することが出来ました。
※蓄光マスターバッチの割合が多い場合は金型離型時に製品が割れる可能性があります。
製品状態について
■製品の外観はガラスが入ったような印象で、少しザラザラしております。使用用途によりますが、自社製品とはマッチしておりました!!
■撮影する際、部屋を暗くするとすぐに発光が確認できました。
しばらく暗い部屋に置いたままでしたが、それでもしっかり発光していました。
その後一旦明るさは落ち着きますが目視でわかる明るさで安定しますので暗い空間ならば十分だと感じました。
ただ、発光するには蛍光灯や自然光での蓄えが必要ですので、発光しなくなれば光が必要になります。
※自社製品「キューブボックスα 木扉鍵付き」では現在、蓄光プラスチック樹脂を用いた蓄光シリーズは販売しておりません・・・