2014年7月25日
多発する問題は強度と白化射出成形で開閉式ケースや蓋付き容器などを成形する場合、本体とフタを一体で成形し薄肉のヒンジでつなぐことがありますが、ヒンジ部の金型設計には少し注意が必要です。
よく発生する問題として以下のようなものがあります。
①一見しっかり繋がっているように見えるが数回折り曲げると亀裂が入り割れてしまう。
②思ったような硬さに仕上がらない。
③折り曲げると白化してしまう。
ヒンジの設計で一番重要なのはヒンジ部の強度の問題です。
不良原因は概ね「ウェルドライン」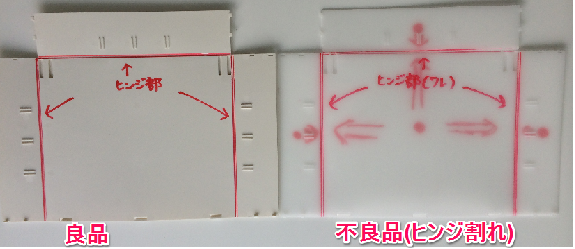
ヒンジがどの程度持てばいいのかは物にもよると思いますが、数十回程度で割れてしまうような場合はその原因のほとんどがウエルドにあるといっていいでしょう。
フタと本体にそれぞれゲートを設けたときその位置関係に注意が必要です。樹脂は流れやすいところから先に流れる傾向があります。
ですから最も樹脂が流れにくいヒンジ部が一番最後となってしまいますのでどうしてもヒンジ部の一番薄いところがウエルド(樹脂どうしの合わせ目)
となってしまいます。
うまく成形できない時は、ゲート位置を工夫する理想でいえば本体かフタかどちらか一方にゲートを設けるほうがよいでしょう。(樹脂が入りきればですが・・)
それが出来ない場合はどちらかのゲートをヒンジから出来るだけ遠くに設けるか片方のゲートを絞ってやることでウエルドをヒンジ部分からずらしてやることが必要です。
この辺りは形状により経験とカンが必要ですので経験のある金型業者と相談するのがいいでしょう。
(赤いマルはゲート位置)
原料グレードや成形直後のクセ付けも◎折り曲げたときの感触(硬い・柔らいなど)は始めは柔らかめ(ヒンジ肉厚を薄め)からはじめて徐々に金型を削って肉厚を増やしていきます。
感覚の問題ですので少しずつ根気よく詰めていく必要があります。もちろん原料グレードでも変わってきます。PPのヒンジグレードを使うのが一般的です。
とはいえヒンジグレードを使っても樹脂は樹脂ですので180度も折り曲げれば少なからず白化します。
白い原料なら目立ちませんが濃い色の原料だとどうしても目立ってしまいます。
そんな場合はちょっと原始的ですが、成形直後まだ温かいうちに折り曲げてクセをつけてあげるのが一番ですいずれにしてもインジェクション成形は金型の設計で製品の良し悪しの80%は決まりますのでヒンジ成形品の経験のある金型業者に依頼するのがよいでしょう。
ヒンジ成形でお困りごとがあればご遠慮なくご相談ください。
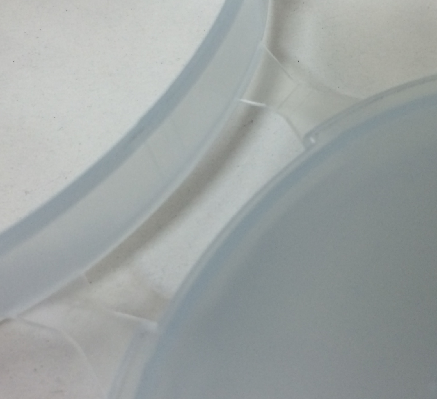